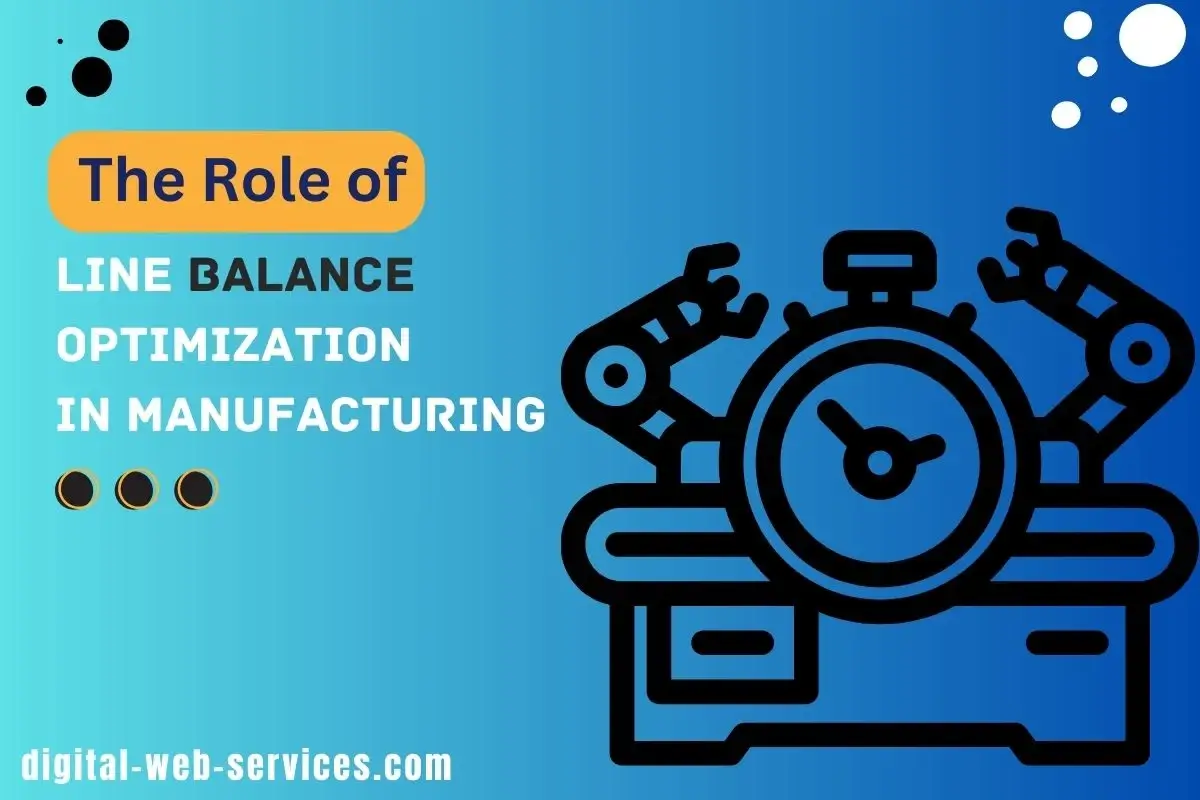
Manufacturers are under constant pressure to deliver products faster and at lower costs, while continuously improving their operational efficiency and product quality so that they can better meet customer demands and remain competitive. Operational excellence is the goal that all manufacturing companies strive to achieve so it can mean different things to different people.
However, as a general way of thinking, it is the relentless pursuit of performance across all levels of the organization. It’s a philosophy of the workplace where problem solving, teamwork, and leadership results in ongoing improvement. At the heart of operational excellence is streamlining, and while there are different philosophies surrounding this, they all invariably involve the continuous improvement of processes and products in an effort to deliver them at the highest quality and minimum cost. At its core its goal is the reduction of waste and the increase in efficiency.
One of the most important factors in operational excellence in manufacturing is line balance optimization. Line balance optimization is the optimal allocation of resources and tasks to achieve a balanced production line. This blog will explore line balance optimization including the definition, benefits, methods for balancing lines, steps for line balance optimizations, the role of line balance optimization software, and overcoming implementation challenges.
What Is Operational Excellence and Why Is It Important in Manufacturing?
Operational excellence is a philosophy, an organizational culture, the state of readiness at all times that sets a standard for your global competitors. Your ability to provide your respective customers and your organization the highest, most consistent system of delivering product or service to meet or exceed customer expectations.
At the most basic level, operational excellence is about streamlining a manufacturing company’s internal processes and products in an effort to deliver the highest quality goods to customers at minimum cost and waste. It takes into consideration just about every part of the organization and its leadership will typically manage the organization in such a way that people are motivated and empowered to continuously improve. Operational excellence contributes to the increased profitability and return on sales with leading revenue and cost positions and reduced waste of valuable resources and a higher quality of products and services.
By focusing on operational excellence, manufacturing companies will reduce operating costs, improve workforce productivity, shorten cycle times and reduce time-to-market and improve pricing flexibility and delivery performance.
A Basic Overview of Line Balance Optimization and Its Relationship to Operational Excellence
Line balance optimization is a method used to balance the allocation of tasks and resources to a production line in such a way that the line works at the most efficient rate. Through this process, the goal is to distribute the workload evenly among all of the workstations to ensure that no workstation on the line is overloaded and perhaps a more serious problem, that some workstations are not idle while others are working. As a crude rule of thumb, one might say that when a line is perfectly balanced no member of the line is working any harder or faster than any other. The operator at each station shares the overall work content equally.
When a production line is balanced, manufacturers can achieve operational excellence by minimizing waste, improving productivity, reducing production time, and delivering products when they are due.
Some of the most significant benefits of line balance optimization include:
- Improved efficiency: One of the most major benefits of line balance optimization is the overall improved efficiency of a manufacturing production line. Balancing the work between stations on a line can help manufacturers improve productivity, reduce idle time between stations, and maximize the utilization of production line resources and employees.
- Higher quality: By optimizing line balance to limit under and overproduction of parts, optimize the use of line equipment, and reduce the handling of parts, manufacturers are able to produce higher quality parts and reduce the chances of producing defective units.
- Lower costs: Manufacturers are often able to reduce overall per unit production costs by streamlining the overall production process flow and reducing unnecessary handling, transportation, and space requirements.
- Improved employee morale: Balancing a production line can reduce stress and fatigue of production line employees by limiting the tedium of repeating the same motion or task day in and day out.
- Greater customer loyalty: By delivering products on time with fewer defects and at a lower price, manufacturers can enhance customer loyalty and improve customer satisfaction.
Line balance optimization reduces idle time, maximizes resource utilization, and minimizes the time tasks are left incomplete. When tasks are evenly balanced across workstations, manufacturers eliminate bottlenecks and create a continuous flow of production. The outcome is improved efficiency, minimal waiting time, and increased productivity throughout the manufacturing process.
Reduced Cycle Times, Increased Throughput
Balancing the workload from the start to the end of the production process reduces the time a production cycle will take to complete. Tasks will now be divided among workstations with no imbalances, which eliminates idle time. This means that manufacturers can get faster cycle times, increased throughput, and ultimately meet customer demands more effectively.
Enhanced Product Quality, Customer Satisfaction
A balanced production line eliminates overburdened workstations that can compromise product quality. Consistent completion of tasks on a balanced line can improve product quality over time. This means fewer errors at workstations, and will ultimately ensure that the customer is satisfied every time they open a product.
Resource Allocation Flexibility
Line balance optimization lets manufacturers schedule the exact number of staff needed to get the job done at the right time. This means that employees are scheduled according to how much work there is to be done each day. Manufacturers can add or take away staff as demand fluctuates. This type of workforce allocation means that manufacturers can keep production at peak efficiency, without over- or understaffing, while reducing costs all along the line.
Understanding Line Balancing Methods
Line balancing methods are a structured approach for a manufacturer to use to divide tasks among workstations. The line balancing methods help manufacturers determine the optimal assignment of tasks to create a line that’s as close to being perfectly balanced as possible. The key objective of line balancing methods is to reduce idle time and improve resource utilization by evenly distributing the work among workstations.
V-Curve Strategy – The V-Curve strategy involves analyzing the production process, distributing a round of tasks of equal complexity and then adjusting staff accordingly. The idea is to attempt to work forward by distributing some tasks to the right due to the fact that they’re easier than the remaining tasks, fulfilled, and then work back to the left to get the balance right.
The Ranked Positional Weight
The Ranked Positional Weight (RPW) method assigns weights to different workstations based on their position in the production line and workload requirements. Workstations with higher weights are assigned more tasks and those with lower weights are assigned fewer tasks. The Heuristic or Trial and Error method involves a trial and error approach to achieve line balance. Manufacturers make adjustments to task assignments, evaluating the impact on line balance, and repeating until an optimal solution is reached.
Evaluation of Each Method’s Strengths and Limitations
The V-Curve strategy is a logical, step-by-step approach that ensures maximum utilization of resources. It focuses on completing as many tasks as possible at each station to prevent bottlenecks elsewhere, utilizing materials and operator time effectively. The RPW method takes into consideration the position of the workstations when assigning tasks, ensuring efficient task allocation. In contrast, the Heuristic method is more flexible although its foundation is less systematic. Adjustments can be easily made and new approaches attempted. This method can also be considerably quicker, though it is likely that multiple iterations will be necessary before an optimal line balance is reached.
Steps to Implement Line Balance Optimization
Analyze the Production Process and Identify Bottlenecks – Understanding the existing production process is necessary in order to identify areas requiring improvement and bottlenecks. By analyzing every activity, task durations, possible constraints, etc. companies can calculate the existing time and while collecting data for up to one week on resource utilization. This will help in identifying any inefficiencies and imbalances in the production line set up within this time period.
Set Production Line Standards and Define Desired Cycle Time – By defining and highlighting the time taken for each task and quality standards you have set the benchmarks of your production line in getting the tasks completed as per your requirement. The desired cycle time is defined so that the production is based on your customer requirements like considering existing or forecasted customer demand. By doing so you will be able to match the tasks assigned to the production line and make adjustments at any given time frame.
Assign Tasks and Determine Workload Using Line Balancing Methods – By utilizing these different methods, the complexity and duration is used and capacity decides the tasks allocation to different workstations in the production line. Here you need to also note that ensuring the tasks are correctly balanced is possible, ensuring that the total work content that is assigned to any workstation is approximately the same throughout the workday or any other processing time. In recent years, there are different programs that have been made available where it has been possible to get a balloon type curve to your workstation.
Adjust Staffing Levels and Ensure Workstation Capacity is Not Exceeded
Balance the line by adjusting staffing levels to suit workload requirements and achieve sufficient line balance. Ensuring that workstations are not over-utilized or burnt out is essential to maintaining an efficient line.
The Role of Line Balancing Software
Why Line Balancing Software is Important for Optimizing Line Balance
The role of line balancing software in optimizing line balance and achieving operational excellence is critical. Line balancing software automates the collection of data, analysis and visualization of the distribution of the workload across workstations, enabling manufacturers to make data-driven decisions more effectively to balance the line.
Features and Benefits of Line Balancing Software
Line balancing software has several features and abundant benefits. For example, it enables real-time monitoring of the status of line balance so that manufacturers can more promptly identify better or worse balance. With data analysis tools, manufacturers can identify which imbalances are most hurting line productivity, and they can identify process changes that would improve line balance fairly simply. Using optimization algorithms, the software determines the distribution of the tasks and workload across workstations with the minimal task and workload time. The line balancing software enhances manufacturing collaboration and communication capability, which is useful for information sharing and team building.
Overcoming Challenges in Line Balance Optimization
Resistance to Change and Employee Buy-in
Supervisors and employees are often accustomed to what tasks are assigned to what workstation, and they may be resistant to those changes. It is important to provide the supervisors and employees with training and support in doing line balancing; and to often communicate in general terms about the benefits that line balancing and other lean improvements are bringing to the employer and therefore them. Such general communications show that management is thinking about these things and why.
Lack of Data and Visibility
Access to accurate and timely data is a must-have for the creation and optimization of the work assignments. The lack of data visibility can impede the performance analysis and improvement of a process even by the most experienced production management experts, engineers and their consultants, who succeed best when they have the greatest help in solving problems in the workplace. By installing data collection systems or line balancing software, manufacturers will be able to have more timely and better data visibility to make more effective management decisions.
Complexity of the Production Process
The production process can be complicated, and there can be many different variables and interdependencies. Draw the process out, and try to disassemble it into smaller portions. This disassembly step helps narrow things down and helps us all (management, employees and their consultants) decipher and understand what to do with the difficult variables, their interdependencies and if they matter or not. It is easier to keep things under control when there are fewer of them to do. It is easier to study these selected variables and sub-processes with industrial engineering, other standard work and especially decent line balancing software, in a manner they can be understood, than with all the algorithms floating around in one’s head.
Fluctuating demand and workload introduce new layers of complexity to line balance optimization. In these instances, it becomes critical for manufacturers to pivot in real time and deploy strategies such as cross-training employees and maintaining variable staffing levels to remain responsive and effective in this pursuit.
Conclusion
Line balance optimization is critically important for manufacturers hoping to realize operational excellence. By distributing work and resources evenly across stations on manufacturing lines, they can drive efficiencies, reduce cycle times, increase product quality, and position themselves to deliver the continuous value and customer satisfaction necessary to stand out in a crowded, ultra-competitive field. Understanding line balancing methods, deploying line balancing software, and avoiding key implementation challenges are necessary steps in the process for realizing the benefits of line balance optimization. Prioritizing line balance optimization is a clear path to enhanced efficiency, and a more productive and efficient organization – all of which is key in the pursuit of operational excellence that is increasingly necessary in a competitive manufacturing space.
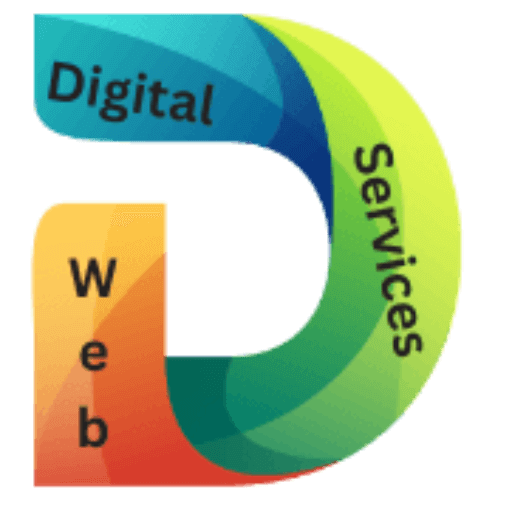
Digital Web Services (DWS) is a leading IT company specializing in Software Development, Web Application Development, Website Designing, and Digital Marketing. Here are providing all kinds of services and solutions for the digital transformation of any business and website.